Revolutionizing Manufacturing: Exploring Smart Manufacturing and Industry 4.0
- Kaustav Engineering
- Mar 28, 2024
- 3 min read
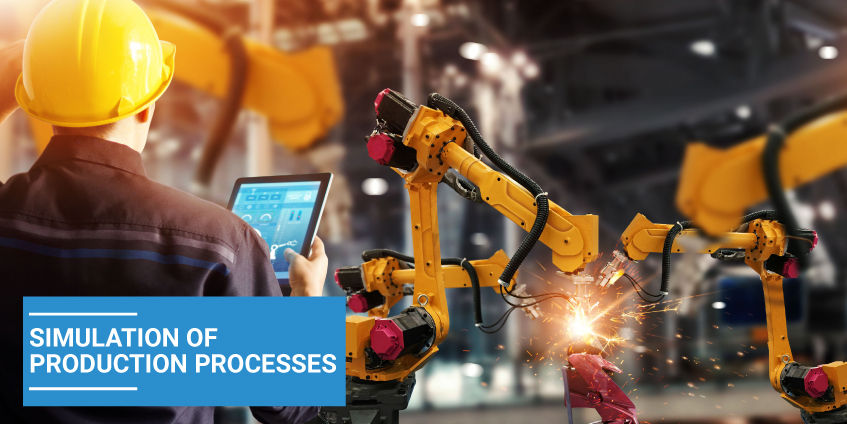
Introduction: In recent years, the manufacturing industry has witnessed a transformative shift driven by advancements in technology and automation. Smart Manufacturing and Industry 4.0 represent the convergence of digital technologies, data analytics, and automation to revolutionize traditional manufacturing processes. This blog explores the key concepts, benefits, and implications of Smart Manufacturing and Industry 4.0 in shaping the future of manufacturing.
Understanding Smart Manufacturing: Smart Manufacturing is a holistic approach to manufacturing that leverages data, connectivity, and automation to optimize the entire manufacturing value chain. It encompasses various technologies and strategies aimed at improving efficiency, flexibility, and productivity while reducing costs and waste. Key components of Smart Manufacturing include :

Internet of Things (IoT): IoT devices and sensors are deployed throughout the manufacturing environment to collect real-time data on equipment performance, production processes, and product quality. This data is then analyzed to optimize operations and enable predictive maintenance.
Data Analytics: Advanced analytics techniques, such as machine learning and artificial intelligence, are used to analyze vast amounts of data generated by IoT devices. These analytics provide insights into production trends, identify potential issues, and support data-driven decision-making.
Cyber-Physical Systems (CPS): CPS integrate physical components with digital systems to create interconnected manufacturing environments. This enables seamless communication between machines, processes, and personnel, facilitating real-time monitoring, control, and optimization of production activities.
Additive Manufacturing: Additive manufacturing, also known as 3D printing, is a key technology in Smart Manufacturing. It allows for the rapid prototyping, customization, and production of complex parts with reduced material waste and lead times.
Exploring Industry 4.0: Industry 4.0, often referred to as the Fourth Industrial Revolution, builds upon the principles of Smart Manufacturing to create interconnected, autonomous, and digitally-enabled manufacturing systems. It represents a paradigm shift in how products are designed, produced, and distributed. Key elements of Industry 4.0 include:
Interconnectedness: Industry 4.0 emphasizes the connectivity of machines, processes, and systems across the entire manufacturing value chain. This interconnectedness enables seamless data exchange and collaboration between various stakeholders, including suppliers, manufacturers, and customers.
Automation and Robotics: Automation and robotics play a central role in Industry 4.0, with autonomous robots performing tasks traditionally carried out by humans. These robots are equipped with sensors, actuators, and AI algorithms to perform complex tasks with precision and efficiency.
Big Data and Analytics: Industry 4.0 relies on big data and advanced analytics to extract actionable insights from vast amounts of manufacturing data. Predictive analytics, machine learning, and AI algorithms are used to optimize production processes, predict maintenance needs, and improve product quality.
Digital Twins: Digital twins are virtual replicas of physical assets, processes, or systems that enable real-time monitoring, simulation, and analysis. They allow manufacturers to simulate and optimize production processes, test new ideas, and identify potential issues before they occur.
Benefits of Smart Manufacturing and Industry 4.0: The adoption of Smart Manufacturing and Industry 4.0 offers numerous benefits for manufacturers, including:
Increased efficiency and productivity through optimized processes and automation
Improved product quality and consistency through real-time monitoring and control
Reduced downtime and maintenance costs through predictive maintenance
Enhanced flexibility and agility to respond to changing market demands
Greater customization and personalization of products to meet customer needs
Improved sustainability through reduced waste, energy consumption, and environmental impact
Implications for the Future: As Smart Manufacturing and Industry 4.0 continue to evolve, they will have far-reaching implications for the future of manufacturing and society as a whole. Some key implications include:
Workforce Transformation: The adoption of automation and digital technologies will require a skilled workforce capable of operating, maintaining, and optimizing advanced manufacturing systems.
Supply Chain Resilience: Smart Manufacturing and Industry 4.0 enable greater visibility and collaboration across supply chains, enhancing resilience and agility in the face of disruptions.
Regulatory and Ethical Considerations: As manufacturing becomes more interconnected and autonomous, there will be increased scrutiny and regulation surrounding data privacy, cybersecurity, and ethical use of AI and automation.
Conclusion: Smart Manufacturing and Industry 4.0 represent a transformative shift in the manufacturing industry, offering unprecedented opportunities for innovation, efficiency, and competitiveness. By embracing these technologies and principles, manufacturers can unlock new levels of productivity, quality, and sustainability, shaping the future of manufacturing for years to come.
Comments